ИММиТ: установки прямого лазерного выращивания, синтез на подложке и другие чудеса науки
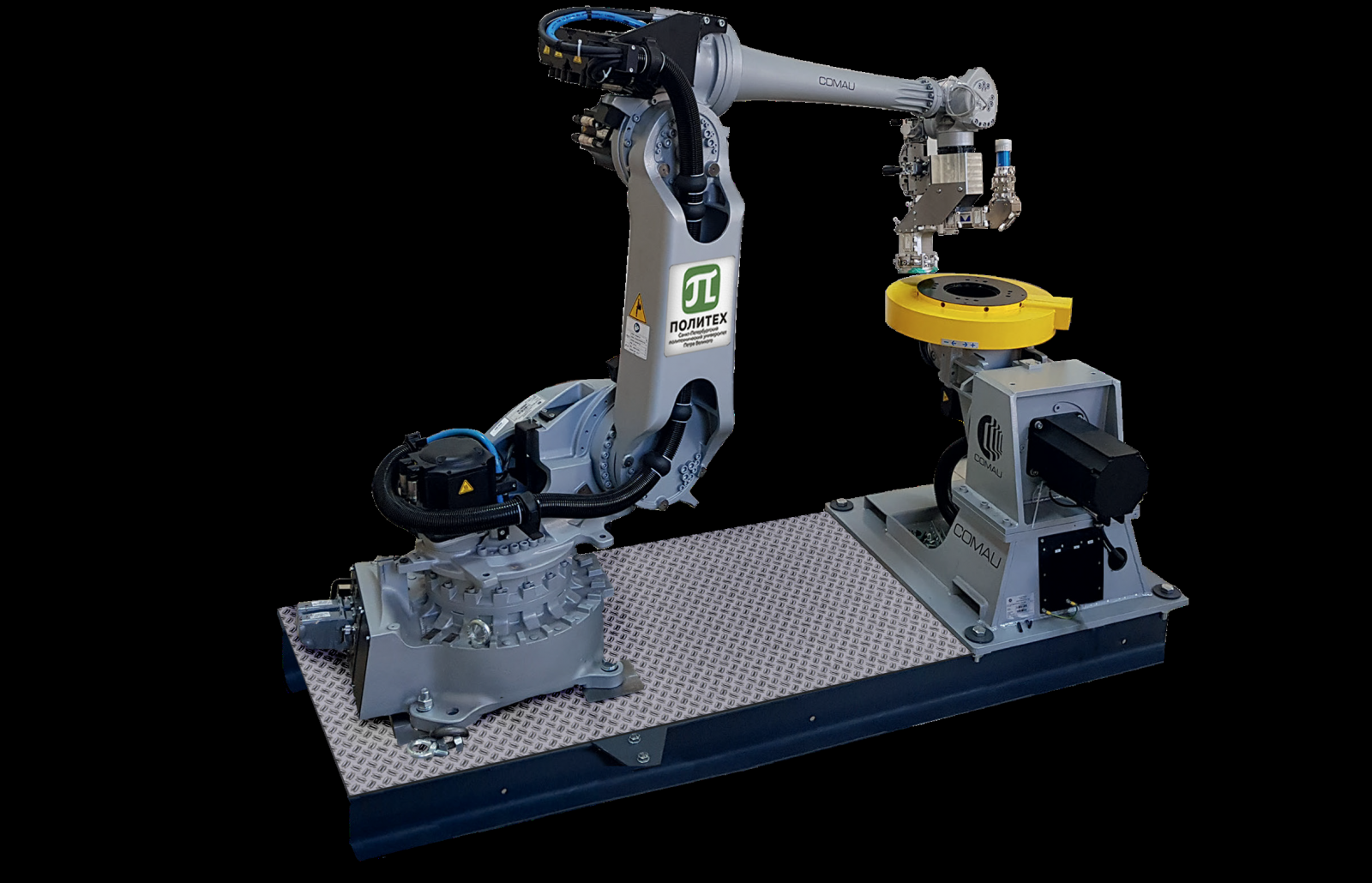
Институт машиностроения, материалов и транспорта (ИММиТ) удерживает лидерские позиции в исследованиях и проектировании новых изделий, разработке конкурентоспособных технологий в обширной области производства – от машиностроения и робототехники до аддитивных технологий, материаловедения и дизайна. О новейших достижениях ИММиТ в научной и практической деятельности рассказывают ведущие специалисты института.
Прямое лазерное выращивание
Дмитрий Масайло, доцент Института металлургии машиностроения и транспорта, Научно-образовательный центр «Конструкционные и функциональные материалы»:
- Я занимаюсь технологией прямого лазерного выращивания по американскому стандарту ASTM – Directed Energy Deposition. В Российском ГОСТе эта технология носит название «Прямой подвод энергии и материла». В качестве источника энергии применяется лазер, электрическая дуга, микроплазма либо электронный луч. Исходными материалами в основном служат порошки. Полгода назад купили специальную наплавочную головку, которая позволяет осуществлять процесс с использованием проволочных материалов. Применение проволоки в качестве исходного материала может серьезно удешевить конечное изделие, по сравнению с использованием порошков. Но ситуация начинает меняться – активно развивается технология получения порошков, а при массовом их производстве она станет экономически более выгодной.
В настоящее время основное преимущество использования металлической проволоки в том, что она имеет сертификаты, а металлические порошки в РФ пока не сертифицированы. Этим вопросом сейчас занимаются исследователи Всероссийского научно-исследовательского института авиационных материалов (ВИАМ). С 2018 года в России работает технический комитет по стандартизации ТК 182 «Аддитивные технологии». Но до сертификации порошков, которые используются в аддитивных технологиях, дело пока не дошло. А проволока у нас давно сертифицирована.
Важно отметить, что аддитивные технологии и сварка – это родственные процессы. Поэтому пути решения различных задач практически всегда одни и те же, за исключением некоторых технологических нюансов.
- В каких сферах применяется технология прямого лазерного выращивания?
- Прежде всего, для ремонта и восстановления изношенных и поврежденных частей изделий, например валов машин и механизмов. Эту работу можно поставить на поток. На однотипных изделиях мы будем каждый раз заменять одну и ту же часть детали, с последующей механической обработкой. Мы можем каждый раз одну и ту же программу выполнять, и это можно все абсолютно автоматизировать. Для чего? Прежде всего, чтобы сократить время восстановления, а также снизить коэффициент брака. Робот, в отличие от человека, ошибиться не может.
Изделия с нуля производить тоже возможно. Но прежде нужно просчитать экономическую целесообразность. На многих предприятиях, где специалисты начинают вникать в аддитивные технологии, но глубоко еще не погружены в тему, пытаются сделать серийное стандартное изделие с помощью 3D-печати и удивляются, что получается значительно дороже, чем по традиционным технологиям.
Если получение детали давно отработано другими технологиями, литьем, ковкой, с последующей механической обработкой, использующей специальную оснастку, то при крупносерийном производстве это получается дешевле. Аддитивные технологии надо использовать для производства уникальных деталей, которые сложно либо вообще невозможно изготовить традиционным способом, а также для производства мелкосерийных изделий. Специалист, который занимается аддитивными технологиями, должен быть и конструктором, и инженером-технологом, и, самое главное, еще и материаловедом. Все надо рассчитывать, чтобы это было целесообразно по сравнению с традиционными способами.
- В чем ключевое преимущество аддитивных технологий?
- Мы можем создавать так называемые градиентные материалы с изменением химического состава изделия и его структуры. Например, шестеренка, у которой поверхность должна быть твердой, а сердцевина вязкой. Для чего? Чтобы снаружи она не изнашивалась, и чтобы не ломалась при высоких нагрузках. Все это делается относительно просто.
Политех разработал две установки прямого лазерного выращивания. Одну – совместно с нашим индустриальным партнером, ее запустили в 2018 году. Первый наш проект был трудоемкий и интересный. Но шишек набили изрядно, так как часто приходилось совмещать несовместимое, вставлять так называемые костыли. Набравшись практического опыта, мы решили сделать что-то свое, со сквозной технологией. Мы взяли за основу программное обеспечение компании Siemens, которое является одним из лучших в мире. Оно позволяет проектировать, моделировать процессы, строить управляющие программы. Взяли логический контроллер Siemens и итальянского робота, но с приводом от компании Siemens. Все это объединили вместе, тем самым добившись максимального функционала, без каких-либо ограничений.
Вторую установку сделали универсальной со сменными головками. Это основной орган, который фокусирует лазерное излучение и подает строительные материалы. Есть порошковая и проволочная головки, на их смену уходит не более 10 минут.
Наша установка с ЧПУ-управлением использует стандартный открытый G-код. Что это значит? У каждого робота свой язык, специально созданный компанией-разработчиком. Чтобы робота запрограммировать, нужно знать этот язык, а также покупать лицензию на его использование.
Расчет моделирования процесса 3D-печати
Алексей Орлов, научный сотрудник лаборатории «Дизайн материалов и аддитивного производства» Института металлургии, машиностроения и транспорта:
- Основное направление моей деятельности – это проектирование, конструирование и проведение различного рода расчетов. В частности, это расчеты моделирования процесса 3D-печати изделия.
- Для чего нужны предварительные расчеты в данной области?
- Когда мы отрабатываем технологию и начинаем готовить файлы для печати какого-либо изделия, то для минимизации пробных запусков, чтобы отсечь какие-то неполадки при печати и получить конечное изделие с минимальным отклонением от исходной геометрии, предварительно выполняем расчеты. Используем лицензированные CAD/CAM программы.
- Как это применяется на практике?
- 3D-моделирование часто используется для реверс-инжиниринга, когда есть какая-то деталь, которая изготавливается традиционным способом, но нет на нее никакой документации. Мы сканируем готовое изделие, создаем 3D-модель и по ней готовим необходимую документацию. Очень часто стоит задача, когда у нас есть изделие, которое изготавливается с помощью фрезерной или токарной обработки, а заказчик хочет перейти на аддитивное производство, так как ему требуются малые партии изделий. При этом изготавливать детали, спроектированные под традиционную технологию, с одной стороны, не совсем целесообразно, а с другой стороны – материалоемкость при использовании аддитивных технологий снижается.
С помощью аддитивных технологий мы можем получить более сложное по геометрии изделие, которое не всегда можно получить традиционными методами обработки. Например, сетчатые конструкции, изделия с внутренними полостями или сложными каналами охлаждения. Все это можно сделать за один технологический цикл.
Мы проводим оптимизацию 3D-модели под производство именно по аддитивной технологии. Делается топологическая оптимизация и изделие приобретает более плавные очертания, так называемый «бионический дизайн». Плюс ко всему: за счет топологической оптимизации повышается коэффициент использования порошка.
- В связи с санкциями, поставки многих изделий и комплектующих прекратились. Поэтому единственный вариант сохранить работоспособность оборудования – это развитие импортозамещения.
- В целом с импортозамещением, с изготовлением и ремонтом деталей это очень актуально, мы используем реверс-инжиниринг. Даже когда изделие выработало свой срок, например, на валах появился износ, поломки произошли в зубчатом венце шестерни, то технологии прямого лазерного выращивания позволяют отремонтировать это изделие, выполнить наплавку, восстановить его геометрию. Для этого пишется программа обработки.
- Какие перспективные работы ведутся сейчас?
- Важная последняя работа – в области сетчатых конструкций. В рамках Федеральной целевой программы, которая длилась в течение трех лет, мы исследовали ячеистые конструкции, их влияние на механические характеристики изделий. В медицине это привело к созданию ячеистых имплантатов.
Почему это актуально? Если использовать сплошной материал, то имплантат получается более жесткий по сравнению с берцовой костью человека. К чему это приводит? При нагрузках начинается негативное воздействие имплантата на кость, и она начинает разрушаться. Наша идея заключалась в том, чтобы жесткость конечного изделия (имплантата) была схожа по механическим характеристикам со свойствами кости. Для этого и создали ячеистую структуру. Когда вставили имплантат в кость, то при нагрузках они стали работать как единое целое. Ячеистая структура имплантата позволяет тканям быстро в него врастать. Корсетные материалы мы научились делать с заданными механическими характеристиками.
Структура может влиять на свойства материала. Мы можем за один технологический цикл сделать изделие с разными свойствами. Например, замковая часть турбинной лопатки у нас обладает мелкодисперсной структурой, а в пере – направленные вытянутые зерна. Это позволяет значительно увеличить ресурс турбинной лопатки. При этом изделие не требует дальнейшей постобработки и обладает требуемыми функциональными свойствами в разных зонах. Получается, что материал один, а структура – разная.
Аддитивные технологии позволяют использовать в процессе изготовления материалы с различным химическим составом. Моя задача – посмотреть, спроектировать, рассчитать, что получится в результате.
Сейчас продолжается проект с Росатомом. Изделия имеют специальную ячеистую структуру, уникальную тем, что обладают малым модулем упругости, который требуется для работы самого изделия.
- Какие технологии 3D-печати используются в лаборатории?
- В нашей лаборатории есть несколько направлений по аддитивным технологиям: послойный синтез, прямое лазерное выращивание, работаем с металлами, также есть направление по керамике, а недавно появилось оборудование по пластику.
Мы разработали свою собственную установку по лазерному выращиванию. Титановые сплавы достаточно капризные, и они требуют использования защитной газовой среды. Поэтому приняли решение спроектировать камеру для создания локальной атмосферы. Передо мной возникла задача – посчитать газовые потоки внутри камеры и определить их максимально эффективное использование. Я провел ряд расчетов газовых потоков, выбрал наилучший вариант, который и будем применять в работе. Установка работает уже продолжительное время и помогает решать уникальные задачи по импортозамещению.
Печать керамических изделий
Вадим Суфияров, доцент Научно-образовательного центра «Конструкционные и функциональные материалы» ИММиТ, ведущий научный сотрудник лаборатории «Синтез новых материалов и конструкций»:
- Какие технологии применяются для 3D-печати керамики?
- Мы последовательно освоили аддитивное производство полимеров после металлов, и теперь перешли к керамическим и композиционным материалам. Направление, связанное с производством керамических изделий и композитных материалов, становится крайне актуальным, поскольку позволяет получить изделия с уникальными свойствами. Подход в керамических системах значительно отличается от 3D-печати полимеров или металлов.
Разные техпроцессы аддитивного производства могут использоваться для печати керамических изделий. Но все они идут через связующее вещество. 3D-печать выполняется керамическим порошком, частицы которого объединяются связующим составом.
После 3D-печати получается заготовка или так называемая грин-модель. На этом этапе изделие не обладает какими-либо особыми характеристиками по прочности и функциональности. Поэтому проводится последующая обработка материала. Как правило, на первом этапе постобработки производится термическая обработка грин-модели для удаления связующего. В результате получается браун-модель. Изделие сохраняет размеры, но часть массы теряется за счет удаления связующего. После применяются различные варианты процесса консолидации, например это может быть спекание – самый распространенный вариант. При спекании идет уменьшение в размерах за счет усадки. Частички начинают друг с другом взаимодействовать, образовывать перешейки. Впоследствии они консолидируются за счет диффузии атомов и стремления к снижению свободной энергии в результате уменьшения площади поверхности.
Спекание производится при повышенных температурах для интенсификации процесса диффузии и в зависимости от материалов может проводиться в вакууме, инертной среде или на воздухе.
Другой вариант уплотнения заготовки – это инфильтрация. Эта технологическая обработка часто применяется для получения композиционных материалов, когда используется материал с меньшей температурой плавления. При нагревании легкоплавкая составляющая расплавляется, и за счет действия капиллярных сил заполняют пустоты в браун-модели. При этой процедуре геометрические размеры изделия сохраняются – нет усадки.
- Каковы перспективы применения керамики?- Перспективность композитной керамики – в возможности широкого применения. Анализируя научные публикации, мы выделили два приоритетных направления. Во-первых, создание пористых структур с управляемой (контролируемой) пористостью. Это направление актуально в областях, где требуется высокая удельная поверхность, программируемые пористые структуры. Это может применяться в нефтехимической отрасли, металлургии, автомобилестроении.
Активно ведутся исследования в области применения композиционных материалов, таких как карбид кремния и карбид бора. Они крайне актуальны для создания деталей авиационных газотурбинных и ракетных двигателей – создание нового поколения материалов, которые выдерживают высокие температуры. Перспективным является использование таких материалов в атомной промышленности. Изделия, созданные на базе карбида кремния или карбида бора, выдерживают радиацию и высокую температуру.
Другое направление – создание функциональной керамики. Например, совместно с Росатомом мы развиваем проект по изготовлению пьезокерамических изделий. Пьезокерамика известна тем, что при механическом воздействии она способна генерировать электрический ток, и наоборот, воздействуя на нее электрическим потенциалом, изменяем ее размер. Причем характерно, что она это может делать очень быстро. Эта особенность используется в датчиках давления и как источник ультразвука. Основные области применения пьезокерамики: ультразвуковые приборы, медицинские, дефектоскопы, эхолоты – они используют для генерации ультразвука пьезоэлементы. Сейчас есть определенный тренд по переходу от использования свинцовой пьезокерамики к более безопасной безсвинцовой. Мы разработали технологию синтеза порошкового материала безсвинцовой пьезокерамики под 3D-печать, отработали технологию 3D-печати из этого материала и спекания, провели исследование его свойств. Сейчас мы планируем изготовить прототип пьезоэлемента для медицинского ультразвукового устройства.
Идет также работа по использованию методов аддитивного производства с керамическими материалами для изготовления вспомогательных элементов для традиционных металлургических процессов. В частности, сейчас ведется исследование по разработке технологии изготовления керамических стержней. Данные элементы имеют сложную геометрию и используются при изготовлении лопаток газотурбинных двигателей 1-2 ступеней турбины. Керамические стержни используются при литье методом направленной кристаллизации, после литья лопаток они удаляются для создания сети каналов, через которые движется сжатый воздух, охлаждающий материал и создающий «рубашку охлаждения» вокруг лопатки. Керамические стержни полностью повторяют сложную сеть каналов охлаждения этих лопаток. Метод 3D-печати позволяет изготовить сложные по геометрии изделия. Материал мы тоже специальный подбирали, чтобы он имел требуемые свойства при последующей технологической обработке, чтобы и температуру держал при литье, и впоследствии мог быть достаточно легко удален из отливки.
Для синтеза композиционных материалов используются преимущества порошковой металлургии, а именно возможность равномерно распределить в матрице частицы другого материала, как правило, керамические частицы – нано- или микроразмерные. Если мы формируем изделие традиционным литьем, то проблематично сделать равномерное распределение различных материалов, поскольку металл расплавляем, более легкие частицы всплывают, поэтому надо перемешивать, в процессе затвердевания надо все контролировать. Практически это невозможно реализовать, при порошковой металлургии это делается проще, а с использованием 3D-печати можно создавать изделия сложной геометрии.
Возможно изготовление уникальных композиционных полимер-керамических, полимер-металлических материалов с помощью аддитивного производства. Это позволяет создать изделия с управляемой контролируемой электрической проницаемостью, например для изготовления компонентов радиоэлектронных устройств. Зарубежными исследователями создаются специальные очень сложные геометрические изделия для применения в антеннах сетей пятого поколения 5G. Мы, в свою очередь, также разработали радиопоглощающие материалы для радиотехнических средств и провели апробацию их для 3D-печати сложнопрофильных конструкций.
Технология синтеза на подложке
Евгений Борисов, доцент Научно-образовательного центра «Конструкционные и функциональные материалы», ведущий научный сотрудник лаборатории «Синтез новых материалов и конструкций»:
- Суть технологий синтеза на подложке или Powder Bed Fusion (PBF), как они называются в иностранной литературе, заключается в формировании деталей в толще порошкового материала. Процесс идет следующим образом: на платформу наносится тонкий слой порошка и далее при помощи лазерного или электронного луча происходит сплавление этого порошка в зависимости от ранее разработанной компьютерной модели. Технология позволяет получать изделия сложной формы за счет малого размера источника нагрева и в целом дает больше свободы конфигурации, возможности выбора формы в отличие от традиционных технологий типа литья, механической обработки, в которых существует необходимость в специальной оснастке при изготовлении деталей сложной формы, то есть под каждую новую геометрию нам нужно изготавливать свою оснастку. В случае литья – это литейная форма, стержни и дополнительные приспособления. Используя 3D-печать, мы можем легко менять геометрию детали, привнося небольшие изменения без дополнительных затрат. Это дает свободу конструкторам при их работе совместно со специалистами в области моделирования процессов. Например, в авиации можно сразу смоделировать процессы, происходящие в двигателе. Тут же оптимизировать геометрию элементов планера или двигателя, вырастить готовую деталь и испытать ее.
Спектр используемых материалов достаточно широкий: жаропрочные, конструкционные и нержавеющие стали, никелевые, алюминиевые, кобальтовые и другие сплавы. То есть возможности применения данных технологий очень широки, это авиация, космос, медицина, автомобилестроение. Все области, где требуются или могут потребоваться детали сложной формы в малой серии.
Мы ведем широкую научную работу на тему разработки градиентных материалов. В частности, материалов с переменной микроструктурой. Как известно, различные микроструктуры дают различные свойства. В некоторых случаях при определенных нагрузках, усилиях более оптимальные свойства дает мелкозернистая структура. В других случаях нужны, наоборот, крупные зерна. Особенно в высокотемпературных применениях, двигателях нужны крупные ориентированные зерна с уменьшением количества границ зерен в материале. Соответственно, одним из научных направлений является создание материала с требуемым размером и ориентацией зерен в рамках одного изделия. Это позволяет достичь требуемых свойств с наиболее оптимальным использованием существующих материалов.
Другим важным преимуществом использования данных технологий является возможность сокращения количества деталей в конечном изделии за счет расширения геометрической свободы в изготовлении деталей. Например, по традиционным технологиям используются несколько деталей, а с помощью аддитивных технологий становится возможным объединить их в одну с уменьшением массы и повышением надежности конечного узла.
Еще одно направление – это топологическая оптимизация – создание бионических структур и легковесных структур. Например, традиционно имеется какая-то монолитная деталь, которая изготовлена литьем, сваркой, прокатом и так далее. В данном подходе используется компьютерное моделирование, за счет оптимизации убирается лишний материал, а добавляется, наоборот, там, где он необходим. Получаются ажурные легковесные конструкции, которые затем изготавливаются аддитивным методом. Особенно это актуально для авиации и космонавтики, где существуют особые требования к весу и прочности. Это различные кронштейны, держатели и другие изделия.
3D-печать полимерных композиционных материалов
Антон Сотов, научный сотрудник лаборатории «Дизайн материалов и аддитивного производства», ведущий научный сотрудник лаборатории «Синтез новых материалов и конструкций», кандидат технических наук. Кандидатскую диссертацию защитил по разработке методики проектирования технологии 3D-печати металлических деталей газотурбинных двигателей:
- В конце 2021 года в Политехе открылось новое направление по 3D-печати полимерных композиционных материалов. На данный момент я являюсь ответственным за данное направление. Институт машиностроения, материалов и транспорта закупил 3D-принтеры по технологии 3D-печати полимерных композиционных материалов, армированных непрерывными волокнами. Это современное оборудование, одно из лучших в мире. В данный момент в лаборатории имеются три принтера с разными зонами построения, позволяющие изготавливать изделия различных габаритных размеров, развиваются два направления 3D-печати. Первое – это изготовление изделий с упорядоченной направленной структурой путем печати непрерывными волокнами, что позволяет обеспечить наилучший армирующий эффект.
Второе направление – изготовление изделий из полимерных композиционных материалов, обладающих эффектом памяти формы. Это так называемая 4D-печать. Такие материалы способны запоминать свою форму. При внешнем воздействии на них, например нагревании или охлаждении, они возвращаются в исходное состояние. Один из вариантов применения – это космическая отрасль. Развертываемая конструкция печатается на принтере, складывается компактно, затем отправляется в космос. Под воздействием определенных факторов, в данном случае температуры, мы сможем эти конструкции раскрывать. То есть придавать им ту форму, в которой они должны работать в космосе.
Применение полимерных композиционных материалов также перспективно для авиационной отрасли. Они гораздо легче, чем металлические изделия. Обладают более высокой удельной прочностью. Так как они армированы непрерывными волокнами, то по своим свойствам сопоставимы с некоторыми металлами, в том числе с алюминиевыми сплавами и некоторыми классами нержавеющих сталей.
В нашей лаборатории имеется весь комплекс оборудования для проведения требуемых испытаний для получаемых в результате работы новых материалов, что необходимо, конечно же, для подтверждения физико-механических и функциональных свойств материала. В исследованиях принимают активное участие студенты-магистранты, бакалавры, которые параллельно выполняют свою выпускную квалификационную работу и непосредственно участвуют на всех этапах экспериментов. Студент погружается в тему, изучает технологию, ищет сферы применения материалов, в итоге пишет выпускную квалификационную магистерскую работу и получает опыт работы с 3D-принтерами.
В связи с перестройкой российской экономики главную роль стали играть импортозамещение, освоение инноваций и новейших технологий. ИММиТ успешно внедряет новейшие достижения науки в практику, развивая кооперацию между институтом, промышленностью и бизнесом, готовит специалистов высокого уровня, способных справиться с современными вызовами.